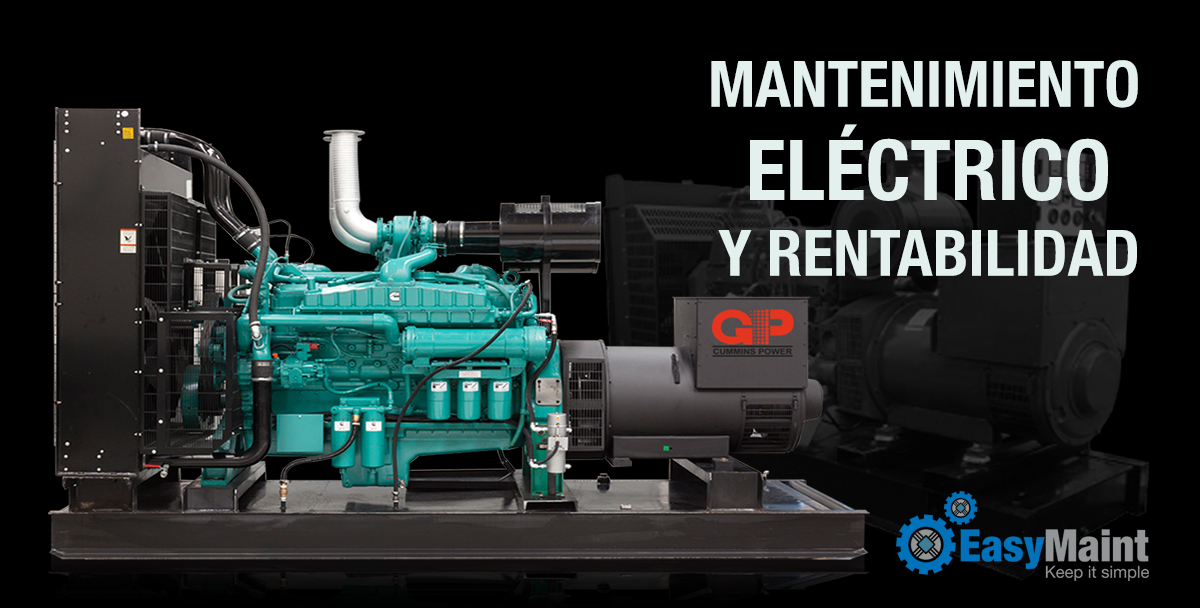
Por Francisco Cano, Product Manager de Servicio en Breakers de Baja Tensión de ABB.
El mantenimiento de los equipos industriales no es un costo para las empresas, sino una inversión. Esa es la premisa con la que se debe partir para entender lo relevante que es definir un programa de control efectivo orientado a evaluar, corregir y anticipar los eventuales problemas que puedan presentar los equipos industriales, con el fin de alargar la vida útil de éstos y disminuir los gastos que producen las fallas inesperadas.
El buen cuidado de los equipos y las precauciones que se deben tener presentes es un tema que preocupa principalmente a proveedores tecnológicos, profesionales del rubro y universitarios, a quienes desde el inicio de sus estudios se les enseña a cuantificar y comparar entre costos de mantenimiento y costos de reparación.
No cabe duda de que cada peso invertido en mantenimiento se transforma en muchos pesos de utilidades para las empresas. Es decir, la forma correcta de proteger los equipos eléctricos es comenzar por coordinar programas de mantenimiento a corto, mediano y largo plazo, con el fin de evitar problemas inesperados que afecten la continuidad operativa de la planta, ahorrando así tiempos y costos en materia de producción.
Todos quienes trabajen con equipos y máquinas deben aumentar la confiabilidad operativa de su negocio; por eso es bueno reiterar que es fundamental que internalicen la idea de que el mantenimiento de los equipos industriales no es un costo para las compañías, sino un ahorro futuro en los costos de producción.
Proceso de relevancia para todos los sectores de la industria
La mayoría de los procesos industriales, ya sea en el rubro minero, de generación, pulpa y papel o bien petróleo y gas, dependen del buen funcionamiento de sus sistemas eléctricos para el desarrollo de su operación. La solución de una falla inesperada de algún sistema o equipo toma un mayor tiempo, debido a que se suman otros factores para solucionar el problema, tales como los tiempos logísticos de repuestos, tiempo de llegada de los técnicos de servicio, etc. Esos tiempos extras afectan directamente a la continuidad operativa de la planta, lo cual se traduce en dinero que se deja de percibir durante un tiempo determinado (y que ya no es recuperable).
Por ello, asegurar la confiabilidad del equipamiento eléctrico de una planta pasa por mucho más que la aplicación de una serie de técnicas, ya que implica llevar un equipo a su punto óptimo de operación. Esto incluye, por ejemplo, determinar el punto de carga en que sufrirá un menor desgaste o daño; establecer si resistirá a un evento de determinada exigencia; analizar previamente el tiempo en que puede estar sometido a ese tipo de esfuerzos, entre muchos otros procedimientos.
Muchas veces ocurre que los operarios relegan el mantenimiento, sin darle real prioridad. Dejar que transcurran días o semanas sin evaluar los equipos suele acarrear efectos irreversibles en éstos. En cambio, una adecuada gestión de mantenimiento disminuye los tiempos muertos de la máquina y costos asociados a instalaciones, traslados y pago a otras empresas por un servicio de reparación.
Por otra parte, una mirada sistemática de los equipos permite determinar la función que cumple en la cadena productiva de la planta y cuál es el impacto que su falla provocaría. Con esto, se determina la criticidad de cada uno de los dispositivos que componen un proceso desde el punto de vista de éstos y ordenar así la prioridad de disponibilidad de uno sobre otro.
Las técnicas aplicadas y conceptos asociados al mantenimiento eléctrico buscan principalmente que los equipos estén la mayor cantidad de tiempo en funcionamiento, que los espacios entre la ocurrencia de una y otra falla sean lo suficientemente amplios y que si existe un desperfecto los plazos de reparaciones sean los mínimos posibles. En general, la disponibilidad de los sistemas eléctricos debería ser cercana al 100%, ya que se trata de tecnologías estáticas, a diferencia de los equipos mecánicos que llegan al 85%. Sin embargo, muchas veces esto no se consigue.
Lo recomendable es que las empresas adapten métodos que se ajusten a sus necesidades, pues el mantenimiento pasa por la definición del nivel de criticidad de las instalaciones y de los procesos. Por ejemplo, para un taller semi-industrial que un motor no funcione por una falla puede que no sea tan crítico, ya que pudiera terminarse el proceso vía manual, lo que no ocurre en un molino para una minera, o con un transformador para una distribuidora. Para cada operación, el nivel de servicio o continuidad es distinto. Otro tema a analiza es si la empresa cuenta con dispositivos de respaldo que permitan sacar un equipo y revisarlo sin afectar el proceso. Todos estos factores se deben estudiar para determinar la estrategia de mantenimiento a aplicar.
Finalmente, el mantenimiento eléctrico permitirá cumplir con los indicadores de desempeño que ha fijado el cliente en su compañía, otorgando mayor disponibilidad y confiabilidad a sus equipos y con ello a sus sistemas y procesos; obteniendo como resultado una mejora en sus costos globales y rentabilizar al máximo sus activos al disponer de un mayor tiempo de producción.