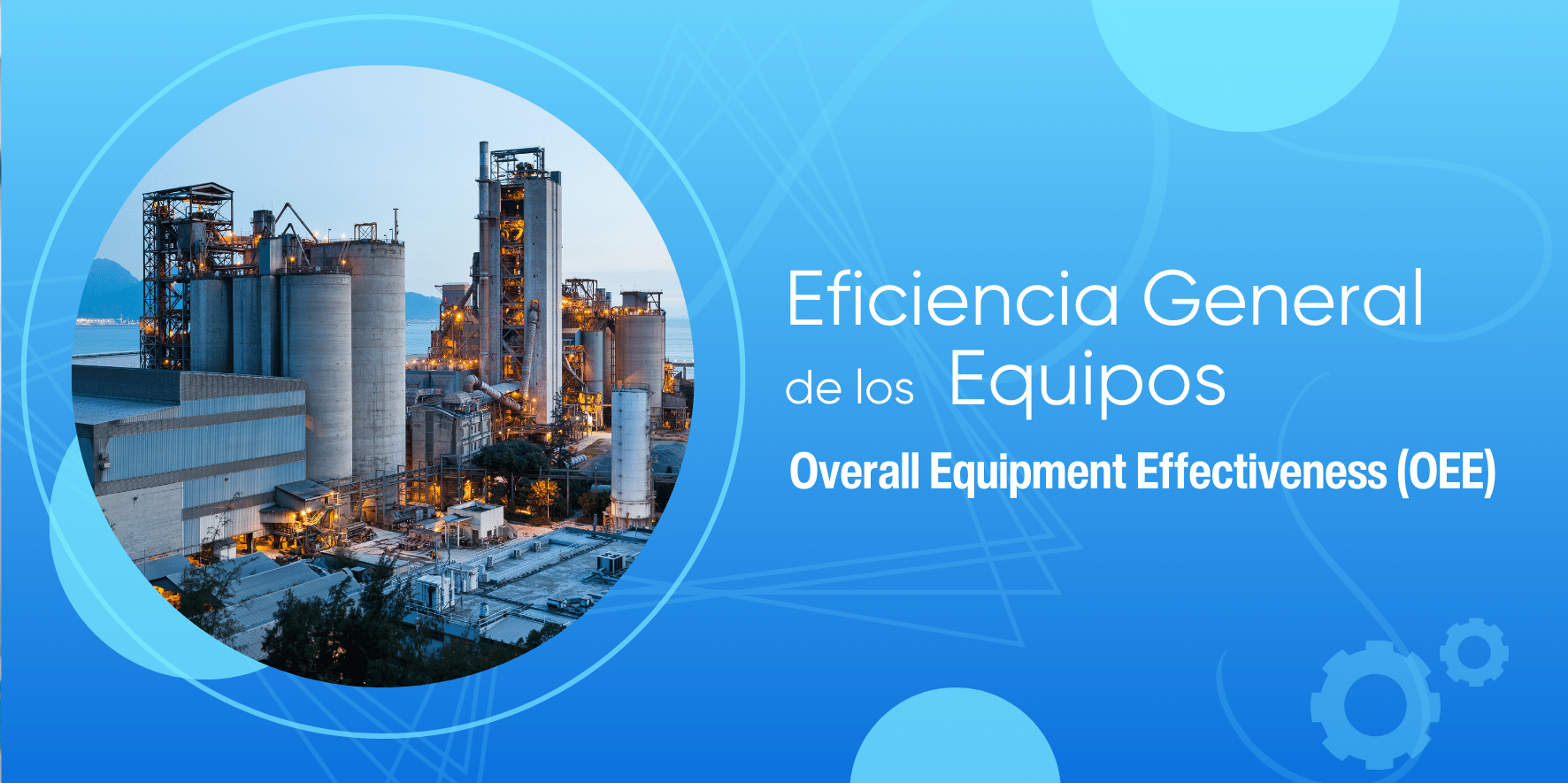
Extracto del artículo «Una herramienta de mejora, el OEE (Efectividad Global del Equipo- Hugo Leonel Alonzo González)
En el presente artículo se definen los conceptos de Efectividad Global del Equipamiento (OEE) como herramienta de mejora continua, enmarcado en la industria manufacturera actual y su relación con el Mantenimiento Productivo Total (TPM), y cómo el mismo mide a diferencia de otros indicadores en un solo Ratio el porcentaje de efectividad de las máquinas y líneas con respecto a su máquina ideal equivalente; el cual es calculado combinando tres elementos asociados a cualquier proceso de producción: Disponibilidad, Rendimiento y Calidad. Esta clasificación proviene de la filosofía del TPM, en la que se definen “Seis Grandes Pérdidas”. Estas pérdidas hacen reducir el tiempo efectivo del proceso y la producción óptima a alcanzar y por lo tanto la elevación del costo de producción.
OEE es el acrónimo para Efectividad Global del Equipo (en inglés Overall Equipment Effectiveness) y muestra el porcentaje de efectividad de una máquina con respecto a su máquina ideal equivalente. La diferencia la constituyen las pérdidas de tiempo, las pérdidas de velocidad y las pérdidas de calidad.
El concepto de OEE nace como un KPI (Key Performance Indicator, en español Indicador Clave de Desempeño) asociado a un programa estándar de mejora de la producción llamado TPM (Total Productive Maintenance – Management, en español Mantenimiento Productivo Total). El objetivo principal del programa TPM es la reducción de costos.
OEE y su relación con el TPM
El OEE mide la efectividad de las máquinas y líneas a través de un porcentaje, que es calculado combinando tres elementos asociados a cualquier proceso de producción:
- Disponibilidad: tiempo real de la máquina produciendo
- Rendimiento: producción real de la máquina en un determinado periodo de tiempo.
- Calidad: producción sin defectos generada
Al mismo tiempo, el OEE analiza y califica los diferentes tipos de pérdidas que pueden producirse en un proceso productivo. Esta clasificación proviene de la misma manera del TPM, en el que se definen “Seis Grandes Pérdidas”. Estas pérdidas hacen reducir el tiempo efectivo de proceso y la producción óptima a alcanzar.
Disminución de Disponibilidad
Pérdidas de Tiempo:
La pérdida de tiempo se define como el tiempo durante el cual la máquina debería haber estado produciendo pero no lo ha estado: Ningún producto sale de la máquina. Las pérdidas son:
Averías (Primera Pérdida): Un repentino e inesperado fallo o avería genera una pérdida en el tiempo de producción.
Esperas (Segunda Pérdida): El tiempo de producción se reduce también cuando la máquina está en espera. La máquina puede quedarse en estado de espera por varios motivos, por ejemplo; debido a un cambio, por mantenimiento, o por un paro para ir a merendar o almorzar.
Disminución de Rendimiento
Pérdidas de Velocidad: Una pérdida de velocidad implica que la máquina está funcionando pero no a su velocidad máxima. Existen dos tipos de pérdidas de velocidad:
Microparadas (Tercera Pérdida): Cuando una máquina tiene interrupciones cortas y no trabaja a velocidad constante.
Velocidad Reducida (Cuarta Pérdida): La velocidad reducida es la diferencia entre la velocidad fijada en la actualidad y la velocidad teórica o de diseño.
Disminución de Calidad
La pérdida de calidad ocurre cuando la máquina fabrica productos que no son buenos a la primera. Se pueden diferenciar dos tipos de pérdidas de calidad:
Deshechos (Scrap) (Quinta Pérdida): Deshechos son aquellos productos que no cumplen los requisitos establecidos por calidad.
Retrabajo (Sexta Pérdida): Los productos retrabajados son también productos que no cumplen los requisitos de calidad desde la primera vez, pero pueden ser reprocesados y convertidos en productos de buena calidad.
“Medir es Conocer”
Debido a que se ha visto que la producción diaria no se corresponde con la situación ideal, es necesario mostrar las desviaciones y buscar la forma de eliminarlas. El conseguir y obtener de forma clara las Seis Grandes Pérdidas – la diferencia entre la situación ideal y la actual – es por tanto el primer paso para empezar a mejorar. Al utilizar una metodología estandarizada para medir las Seis Grandes Pérdidas, los tecnólogos pueden centrar su atención en las mismas para su eliminación ya que una vez conocidas no serán admisibles.
La mayoría de los sectores industriales utilizan métodos de medición para su maquinaria destinada a la producción. Cantidades como el tiempo disponible, las unidades producidas, y algunas veces las velocidad de producción suelen ser el objeto de estas mediciones. Estos métodos son herramientas útiles para aquellos que desean conocer qué produce la máquina.
El TPM trabaja de modo diferente; el TPM no persigue sólo conocer qué ha producido la máquina, sino también que podría haber producido. Este es el motivo por el cual se buscan las pérdidas ocultas.
Objetivo del OEE
Medir el OEE (la Eficiencia Global de Equipo) es una herramienta simple pero poderosa con la que podemos obtener una valiosa información sobre lo que está ocurriendo en la actualidad. El OEE ayuda a los operarios ya que, al reflejar en un documento la evolución de las pérdidas de la máquina, promueve las acciones hacia su eliminación.
Resultados del OEE
El cálculo del OEE genera información diaria sobre el nivel de efectividad de una máquina o conjunto de máquinas. Además, identifica en cuál o cuales de las “Seis Grandes Pérdidas” se debe de centrar el análisis y solución en orden de prioridad. El OEE no es sólo un indicador con el que medir el rendimiento de un sistema productivo, sino que es un instrumento importante para realizar mejoras específicas una vez que ya hemos priorizado las pérdidas.