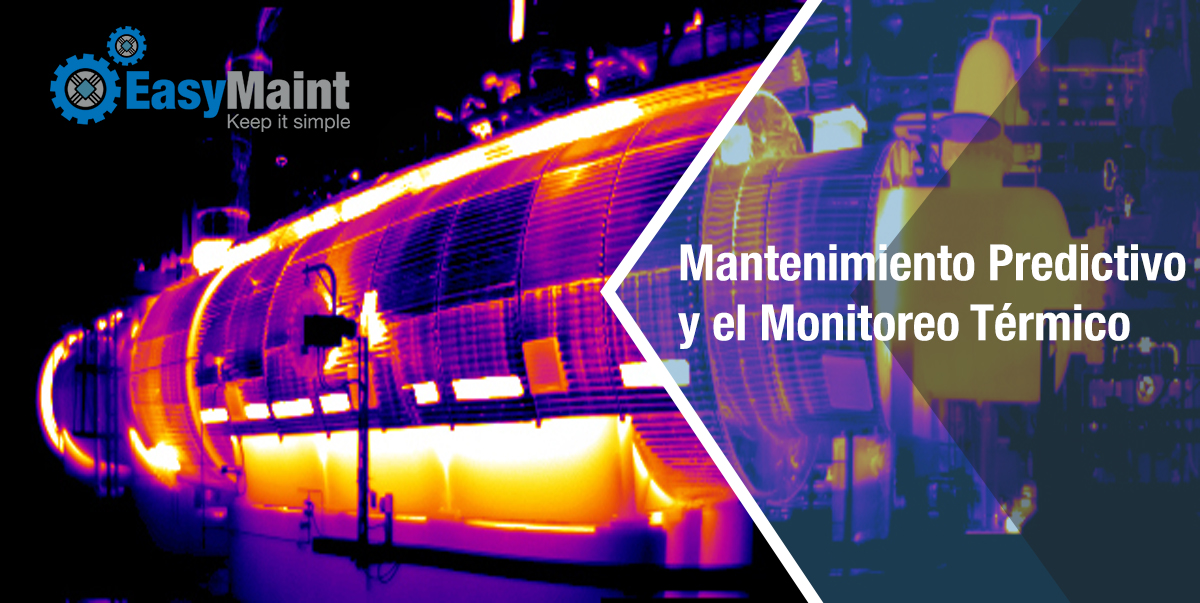
Los sensores infrarrojos se pueden integrar a la perfección con una plataforma de software que reúne datos de muchos otros tipos de sensores.
Independientemente de la industria o las instalaciones, la capacidad de responder más rápidamente a la degradación repentina del rendimiento de los activos reduce el potencial de fallas catastróficas y ayuda a reducir los costos de daños. Durante la última década, los gerentes de mantenimiento han confiado cada vez más en las imágenes térmicas para el mantenimiento preventivo y la solución de problemas en los procesos de fabricación. La razón es simple: el calor a menudo es un indicador temprano de la degradación, y el frío a menudo sugiere fusibles quemados o condensadores fallados. La identificación de patrones térmicos anormales antes de una falla puede ayudar a prolongar la vida útil de los activos y mejorar las capacidades de mantenimiento proactivas de la instalación.
Las cámaras térmicas, también llamadas cámaras infrarrojas, ayudan a los profesionales de mantenimiento, confiabilidad y operaciones a identificar rápidamente los puntos calientes y los puntos fríos que podrían indicar problemas potenciales, ayudándolos a evitar tiempos de inactividad inesperados y daños al equipo. Los técnicos de mantenimiento pueden usar una cámara de infrarrojos para inspeccionar un área completa o un equipo en un momento específico. A medida que se identifican anomalías, el técnico puede concentrarse en áreas irregulares para determinar la magnitud del problema.
Multiplicando las capacidades de imágenes térmicas
Las capacidades mejoradas, la reducción en el costo y la facilidad de uso mejorada que ofrecen las generaciones recientes de cámaras termográficas han mejorado enormemente la capacidad de detectar muchos problemas potenciales que causan errores antes de que causen una falla. El personal de mantenimiento preferiría encontrar un problema inminente que tener que responder a una falla crítica del equipo después de que ocurra.
Esto explica por qué muchas instalaciones están expandiendo su práctica de imágenes térmicas para incluir «monitoreo térmico» con sensores de infrarrojos inalámbricos semifijos y siempre activos. En el pasado, la solución de problemas intermitentes requería que el técnico estuviera en el lugar correcto en el momento adecuado, lo que no siempre era posible. La instalación de sensores de imágenes térmicas semi fijos en múltiples componentes proporciona a los gerentes una visión térmica más completa de los activos de los equipos simultáneamente, en tiempo real durante largos períodos de tiempo, lo que los hace mucho más propensos a detectar fallas intermitentes en el acto.
Los sensores de imágenes térmicas capturan simultáneamente imágenes térmicas de múltiples componentes de motores, ventiladores, bombas y transportadoras para ayudar a detectar patrones térmicos anormales en cojinetes, ejes, cubiertas, correas, cajas de engranajes y otros componentes. Los gerentes pueden comparar estas imágenes a lo largo de todo un ciclo de trabajo para ver qué más está sucediendo cuando aparecen señales de advertencia. Luego pueden responder proactivamente a los problemas y evitar potenciales fallas en otros equipos más adelante. Los sensores de monitoreo térmico brindan más datos para ayudar a los profesionales de mantenimiento y confiabilidad a determinar mejor si necesitan abordar el problema de inmediato o si pueden esperar las horas de menor actividad o hasta el próximo período de mantenimiento programado regularmente.
Cómo funcionan los sensores de imágenes térmicas
Los sensores de imagen térmica semi-fijos funcionan con batería o corriente alterna (AC) y se pueden instalar y mover fácilmente para monitorear el perfil térmico de los diferentes componentes durante largos periodos de tiempo. Se pueden montar en casi cualquier superficie con imanes o discos adhesivos, o se pueden montar utilizando el soporte ajustable incluido con un cardán de 360 grados que permite el posicionamiento en muchos ángulos para capturar objetivos que serían difíciles de alcanzar con una cámara de mano. Para obtener resultados óptimos, los sensores deben montarse a una distancia de 4 a 20 pies del activo. Los usuarios pueden establecer umbrales de temperatura para cada sensor que active alarmas si se exceden esos umbrales.
Cada sensor de monitoreo térmico captura secuencias de imágenes infrarrojas a intervalos especificados por el técnico. Por lo general, es mejor comenzar tomando imágenes a intervalos frecuentes para identificar qué tan rápido cambian las temperaturas de la superficie. Luego, los técnicos pueden ajustar la frecuencia para adaptarse a las necesidades específicas de monitoreo. Por ejemplo, puede comenzar con una imagen por minuto, y si la temperatura de la superficie cambia muy lentamente, puede cambiar la configuración a una imagen cada 30 minutos.
Debido a que todas las imágenes de la secuencia se capturan desde la misma ubicación exacta, el ángulo y la distancia son idénticos. Mediante el uso de software en un dispositivo móvil o PC, los usuarios finales pueden comparar múltiples imágenes del mismo activo o imágenes de múltiples activos tomados simultáneamente para que los puntos calientes y fríos se destaquen. Esto proporciona una imagen más completa de dónde se están gestando problemas y cómo las anomalías térmicas en un componente están afectando a otros activos de producción.
Los sensores de monitoreo térmico se pueden integrar a la perfección con una plataforma de software que reúne datos de muchos otros tipos de sensores, incluidos el voltaje de AC / corriente continua (CC), la corriente, la potencia y la temperatura de contacto. Los usuarios finales pueden asociar las mediciones al equipo, crear jerarquías y seguir las tendencias históricas en el software.
Poner sensores de imágenes térmicas a trabajar
El monitoreo térmico con sensores de cámara infrarroja combinados con sensores de temperatura de contacto, voltaje y corriente, pueden ayudar a resolver problemas y mejorar la confiabilidad de muchos componentes del proceso de fabricación, incluyendo:
Motores, bombas, transmisiones y compresores: la termografía es particularmente útil cuando se monitorean equipos rotativos porque el sobrecalentamiento acompaña a muchas fallas inminentes. Los sensores se pueden instalar en varios motores en una fila, lo que permite a los técnicos de mantenimiento comparar las temperaturas de la superficie y aislar rápidamente los motores con falla (sobrecalentados). De esta forma, los componentes sospechosos pueden repararse o reemplazarse antes de que causen un tiempo de inactividad inesperado.
Instrumentación de proceso: las válvulas, tuberías y mangueras son fundamentales para entregar fluidos a procesos en momentos precisos. Los sensores de imágenes térmicas pueden ayudar a localizar las fugas, la fricción o el exceso de fricción en las válvulas y los tubos. La supervisión térmica proactiva de las tuberías puede ayudar a localizar obstrucciones antes de que falle un circuito completo. El monitoreo térmico también se puede usar para monitorear los niveles de líquido y realizar controles generales de los niveles de material a granel seco en los tanques.
Sistemas de HVAC y condensadores: en los centros de datos, la refrigeración es clave para evitar que los servidores se sobrecalienten. Los sensores de imágenes térmicas se pueden usar para monitorear bastidores de servidores o válvulas y condensadores de calefacción, ventilación y aire acondicionado (HVAC) que se encuentren en el interior. También pueden identificar superficies inusualmente frías que podrían indicar un problema, como un desequilibrio en el sistema HVAC.
Transformadores pequeños: la supervisión térmica puede identificar rápidamente conexiones eléctricas malas, suministro de energía irregular o inadecuado, sobrecargas, armónicos y otras condiciones que preceden a las fallas inminentes del equipo eléctrico.
Pasar de una mentalidad reactiva a una actitud proactiva
La mayoría de las instalaciones albergan componentes aparentemente incontables, desde activos rotativos hasta pequeños transformadores. Perseguir problemas a medida que salen a la superficie pone a prueba incluso a los equipos de mantenimiento más capaces, por lo que es un desafío intentar adelantarse a la ola. Si el personal de mantenimiento es pequeño y se esfuerza constantemente para manejar la última falla del equipo, el tiempo de respuesta puede verse afectado. Como se indicó, las señales de advertencia, como un aumento o disminución significativa de la temperatura de funcionamiento, preceden a la mayoría de los fallos de los equipos. Los sensores de imágenes térmicas y el software de monitoreo de condiciones pueden ayudar al personal de mantenimiento a reconocer los indicadores que pueden llevar al tiempo de inactividad si no se controlan. Esto ayuda a los gerentes de mantenimiento a tomar mejores decisiones sobre los cronogramas de mantenimiento, las órdenes de trabajo y la priorización de situaciones que demandan una respuesta urgente.
Mejora el ROI
El almacenamiento de imágenes térmicas secuenciales y otras mediciones de temperatura, electricidad y calidad de energía crea un rico historial de equipos. Tener estos datos a mano ahorra tiempo en la búsqueda de mediciones de línea de base y permite a los gerentes de mantenimiento realizar evaluaciones más inteligentes.
Al ayudar a los equipos de mantenimiento a detectar una multitud de problemas potenciales antes de que causen fallas, la generación de imágenes térmicas inalámbricas y otros sensores de monitoreo de condición junto con una solución integral de monitoreo de condición pueden hacer que el mantenimiento predictivo sea aún más eficiente.
Recuperado de Accelix (2018) Making predictive maintenance more predictable with thermal monitoring