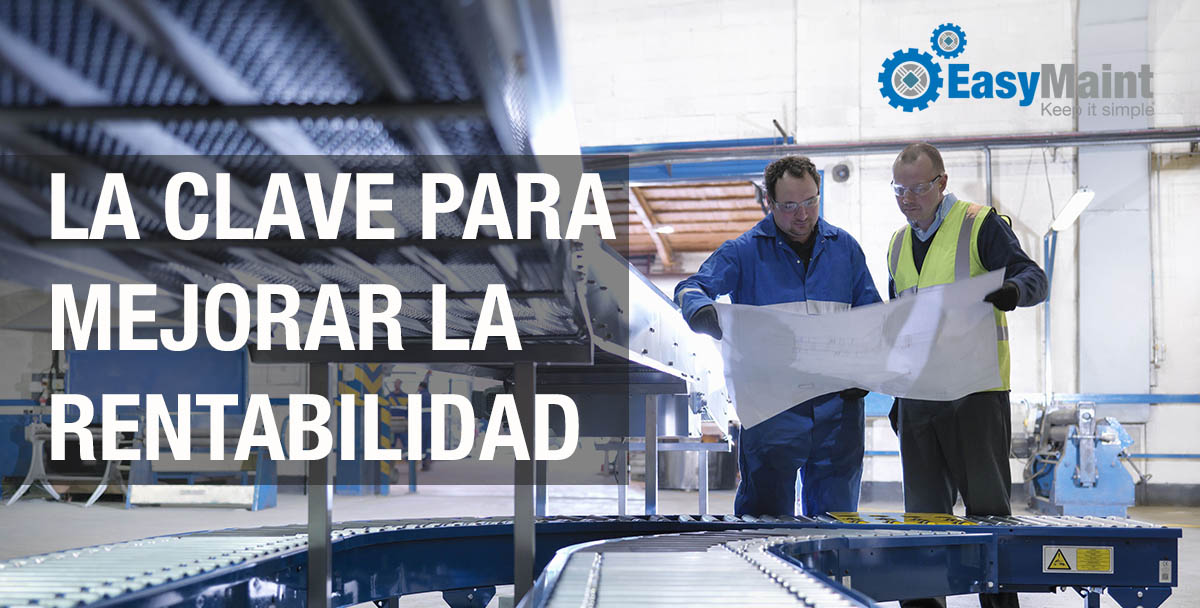
Autor: HishamBinJabar
El mantenimiento adecuado del equipo de la planta puede reducir significativamente el costo operativo general, al tiempo que aumenta la productividad de la planta. Aunque muchos administradores consideran a menudo el mantenimiento de la planta como un gasto, un enfoque más positivo al considerarlo es tomar en cuenta las actividades de mantenimiento como un centro de beneficio. La clave de este método radica en una nueva perspectiva de enfoque de mantenimiento proactivo.
Revisar las maneras más probables de que un equipo falle ha sido una preocupación importante en el mantenimiento centrado en la confiabilidad (RCM) para asegurar que las actividades de mantenimiento proactivo, predictivo y preventivo durante el cambio se podrían planear y llevar a cabo. Con mucha frecuencia el departamento de mantenimiento adoptará un enfoque más cauteloso de trabajar de forma segura y confiar en el método convencional o habitual de mantenimiento del equipo en lugar de probar un método que ha sido probado para ser eficiente sólo para evitar cualquier asunto complicado que surja del método.
Por lo tanto, otra perspectiva de observar la función de mantenimiento no es sólo mantener, sino también mejorar el proceso o el sistema de operación de la planta como resultado de la planificación. Así pues, en lugar de restaurar o tratar de restaurar el equipo a su rendimiento original, la planificación de un cambio podría aún ayudar a mejorar el proceso y el rendimiento de una planta, equipo o cualquier sistema.
En este documento se discutirá sobre otra forma de considerar la función de mantenimiento y cómo maximizar el beneficio potencial de una actividad de mantenimiento. La idea podría ser muy diferente de la filosofía convencional de mantenimiento, pero esto podría ser algo que vale la pena para una nueva perspectiva en este nuevo milenio.
Introducción
La definición de mantenimiento a menudo establece el mantenimiento como una actividad realizada para cualquier equipo para asegurar su confiabilidad para el desempeño de sus funciones. El mantenimiento para la mayoría de las personas es cualquier actividad realizada en un activo para asegurar que el activo continúe realizando sus funciones previstas, o para reparar cualquier equipo que ha fallado, o para mantener el equipo funcionando, o para restaurarlo a su condición de funcionamiento favorable. A lo largo de los años, se han implementado muchas estrategias nuevas como estrategias de mantenimiento destinadas a superar los problemas relacionados con la avería del equipo. Algunas de las estrategias comunes de mantenimiento son las siguientes:
-
Mantenimiento de averías
Este es uno de los primeros programas de mantenimiento que se están implementando en la industria. El enfoque de mantenimiento es totalmente reactivo y sólo actúa cuando el equipo necesita ser fijado. Esta estrategia no tiene ninguna tarea de mantenimiento de rutina y también se describe como carente de alguna estrategia de mantenimiento programada. Para corregir el problema, se realiza un mantenimiento correctivo en el equipo. Por lo tanto, esta actividad puede consistir en reparar, restaurar o reemplazar componentes. La estrategia consiste en aplicar sólo la actividad de mantenimiento correctivo, la cual es necesaria para corregir un fallo que ha ocurrido o está en el proceso de ocurrir.
-
Mantenimiento Preventivo
Esta es una estrategia de mantenimiento basada en el tiempo en la que, sobre una base periódica predeterminada, el equipo se pone fuera de línea, se abre e inspecciona. Basado en la inspección visual, las reparaciones se hacen y el equipo se pone de nuevo en línea. Así, bajo esta estrategia de mantenimiento de equipos, la sustitución, revisión o remanufactura de un artículo se realiza a intervalos fijos, independientemente de su condición en el momento. Aunque esta es una estrategia bien intencionada, el proceso puede ser muy costoso ya que normalmente en el 95% del de las inspecciones todo estaba bien. Sin embargo, es necesario un cierto mantenimiento preventivo ya que algunas regulaciones tales como la regulación de DOSH requieren que la inspección anual/bianual de una caldera sea llevada a cabo.
-
Mantenimiento predictivo
El mantenimiento predictivo es un enfoque más basado en la condición del mantenimiento. El enfoque se basa en la medición de la condición del equipo con el fin de evaluar si un equipo fallará durante algún período futuro, y luego tomar medidas para evitar las consecuencias de esos fallos. Aquí es donde se utilizan tecnologías predictivas (es decir, análisis de vibraciones, termografías de infrarrojos, detección ultrasónica, etc.) para determinar la condición de un equipo y decidir sobre las reparaciones necesarias. Aparte de las tecnologías predictivas, las técnicas estadísticas de control de procesos, la supervisión del rendimiento del equipo o el sentido común del gerente de mantenimiento también son de gran utilidad para monitorear la condición del equipo. Este enfoque es una estrategia económicamente más viable, ya que los trabajos, los materiales y los programas de producción se utilizan mucho más eficientemente.
-
Mantenimiento Proactivo
A diferencia de los tres tipos de estrategias de mantenimiento que se han discutido anteriormente, el mantenimiento proactivo puede considerarse como otro nuevo enfoque de la estrategia de mantenimiento. Diferente al mantenimiento preventivo basado en intervalos de tiempo o mantenimiento predictivo basado en el monitoreo de condiciones, el mantenimiento proactivo se concentra en el monitoreo y corrección de causas de raíz a fallas de equipos. La estrategia de mantenimiento proactivo también está diseñada para extender la edad útil del equipo para alcanzar la etapa de desgaste mediante la adaptación de un alto nivel de maestría de precisión de la operación.
Aparte de estas estrategias de mantenimiento, otros problemas comunes de mantenimiento son los procesos de mantenimiento. En pocos años ha surgido un interés creciente en el campo del Mantenimiento Centrado en la Confiabilidad (RCM). Originalmente desarrollado para la industria de las líneas aéreas, RCM es un proceso estructurado para determinar las estrategias de mantenimiento de equipos requeridas para cualquier activo físico para asegurar que continúe cumpliendo con las funciones previstas en su contexto operativo actual.
Por lo tanto, el objetivo de RCM es determinar el equipo crítico en cualquier proceso, y sobre la base de esta información, diseñar una estrategia de mantenimiento preventivo/predictivo personalizado para la organización. Las iniciativas de RCM, sin embargo, implican una tremenda cantidad de recursos, tiempo y energía. Por lo tanto, el proceso es extremadamente largo y caro.
Otra estrategia que vale la pena mencionar es el Análisis de Fracaso Causa Raíz (RCFA) que se basa en los fracasos que se han producido en el pasado. RCFA toma la acción correctiva más allá de la etapa del componente y en la deficiencia del sistema o etapa de la raíz latente. La mayoría de los costos asociados con la realización de RCFA están en el tiempo y recursos de las personas para verificar los hallazgos. Por lo tanto, RCFA puede ser proactivo cuando se atienden fallas crónicas contenidas en el presupuesto de mantenimiento.
El medio cambiante del mantenimiento
En los últimos años, el mantenimiento se ha vuelto más importante en la industria y el papel del mantenimiento se ha convertido en un objetivo mucho más destacado en la operación de la planta. Desde una simple expectativa de mantener un equipo funcionando o restaurarlo a la condición de operación deseada, la gerencia hoy vio un papel mucho más diferente de mantenimiento.
En la actualidad, la mayoría de los gestores consideran que la eficiencia del mantenimiento es un factor que puede afectar la eficacia y la seguridad de los riesgos, la integridad ambiental, la eficiencia energética, la calidad del producto y el servicio al cliente. Por lo tanto, como el clima de la actividad cambió también lo hace la necesidad de un mejor programa de mantenimiento. En general, la evolución de los cambios de mantenimiento por lo general se clasifica en 3 generaciones diferentes, el período de 1930-1940, que normalmente se refiere como la Primera Generación, entre 1950 a 1970, a menudo se reconoce como la segunda generación, y la década de 1980 hasta el día de hoy que es comúnmente aceptado como La tercera generación.
La evolución en el proceso de mantenimiento también se basa en la complejidad cambiante de la propia industria. La primera generación es los primeros días de industrialización donde la mecanización es baja. La mayoría del equipo en la fábrica era básico y el proceso de reparación y restauración se realizaba en muy poco tiempo. Por lo tanto, el término tiempo de inactividad no importaba mucho y no había necesidad de que los gerentes pusieran el mantenimiento como una cuestión de alta prioridad.
La segunda generación surgió como resultado de la creciente complejidad en el diseño de equipos y plantas. Esto había llevado a incrementar la mecanización y la industria empezaba a depender de estas máquinas complejas. La reparación y la restauración se habían vuelto más difíciles y se necesitaba una habilidad especial y más tiempo para reparar la maquinaria. A medida que crecía esta dependencia, el tiempo de inactividad se hacía más evidente. La gente empezó a pensar que estos fracasos debían ser evitados lo que llevó al concepto de mantenimiento preventivo. Como el costo de mantenimiento comenzó a aumentar bruscamente en relación con otros costos operativos, había un creciente interés en el campo de los sistemas de planificación y control de mantenimiento.
A partir de los años 80, el crecimiento de la mecanización y la automatización se ha vuelto más complejo y algunas pequeñas averías en el equipo podrían afectar el funcionamiento de toda la planta. Esto ha significado que la confiabilidad y la disponibilidad se han convertido en una cuestión clave ya que cualquier falla puede tener graves consecuencias para toda la división.
Bajo los principios de mantenimiento de tercera generación en muchas organizaciones han establecido un plan declarado cero interrupciones/cero fallas en el servicio como sus objetivos de mantenimiento. Sin embargo, dado que ninguna cantidad de mantenimiento puede garantizar la eliminación total de los fallos (siempre hay probabilidad de fallar, pero puede ser muy cercano a cero) ya no es un objetivo realista que es alcanzable, un enfoque más realista es evitar, reducir o eliminar las consecuencias de las fallas.
¿Mantenimiento de Cuarta Generación?
Debido a los rápidos cambios en el desarrollo de equipos y procesos, acelerados con la ayuda de computadoras más rápidas, era sólo cuestión de tiempo cuando el escenario de mantenimiento entró en su cuarta generación. Como se ha comentado anteriormente, el mantenimiento de tercera generación ha experimentado un cambio de enfoque en el mantenimiento para resaltar aquellas áreas en las que el diseño inherente de los activos genera probabilidades de fracasos que son inaceptables y proporcionan cierta orientación y motivación para mejorar esos activos. Por lo tanto, los principios básicos de la cuarta generación de mantenimiento, aunque se basan en las tres generaciones anteriores tienen una característica señalada,
- Deliberación definida del riesgo, especialmente en los niveles más altos de organizaciones, cuando se trata de estrategias de diseño y mantenimiento de equipos
- La coherencia entre la demanda funcional, el diseño del equipo y el mantenimiento es mayor que la integración actual, y
- Hay un rápido desarrollo en la tecnología de la información para detectar, predecir, diagnosticar y prevenir los fallos de los equipos.
Con estos cambios, tal vez el enfoque de mantenimiento va a cambiar y tal vez la nueva misión del departamento de mantenimiento estará más orientada a proporcionar un excelente apoyo a sus clientes, reduciendo la necesidad de mantenimiento.
Otro factor, que podría tener un factor muy influyente en la tendencia de mantenimiento de la cuarta generación, es el creciente uso del modelado informático en la estrategia de mantenimiento. Con el rápido desarrollo de la tecnología informática, especialmente en el área de sistemas artificiales inteligentes y expertos, las simulaciones por ordenador y el modelado pueden proporcionar las herramientas predictivas del futuro. No solo las computadoras ayudan a recolectar y almacenar datos, sino que también nos ayudan a entender mejor la fuente focal de un fallo de equipo.
Costo de mantenimiento
En los últimos años, existe una creciente preocupación por el tema de mayores costos de mantenimiento y productividad de mantenimiento. Según algunas empresas, el mantenimiento es el mayor gasto manejable en la planta: en muchas empresas, superan su beneficio neto anual. Aunque muchos están de acuerdo en que las estrategias de mantenimiento como el programa de mantenimiento preventivo y predictivo se ha demostrado que producen un ahorro de hasta el 25%, el estudio ha demostrado que todavía se puede ahorrar 1/3 de estos costos de mantenimiento. Normalmente, el costo de mantenimiento se puede dividir en dos grupos principales. El primer grupo referido como costos directos son fáciles de justificar e informar. Estos costos directos consisten en artículos tales como mano de obra, materiales, servicios y costos generales de mantenimiento, son el costo tabulado y se muestra como costos de mantenimiento. El otro grupo de costos de mantenimiento son los costos ocultos o indirectos que son más difíciles de medir. Estos costos ocultos de mantenimiento se clasifican como las seis grandes pérdidas:
- Desgloses y pérdidas no programadas de parada de planta
- Precios excesivos de cambios y ajustes
- Paros menores
- Proceso a velocidad reducida
- Pérdidas de inicio y
- Defectos de calidad
Por lo tanto, es muy importante para las empresas maximizar su eficacia de mantenimiento y el tiempo de actividad del equipo. Según un estudio sobre la productividad de mantenimiento, la mayoría de los departamentos de mantenimiento son sólo alrededor del 25% al 35% productivos. Esto hace que muchas empresas experimenten dificultades con el control de calidad, los niveles de producción y la adherencia a la programación, ya que el equipo que están utilizando no se mantiene adecuadamente.
Otro factor, que podría ser muy influyente en la tendencia de mantenimiento de la cuarta generación, es el creciente uso del modelado informático en la estrategia de mantenimiento. Con el rápido desarrollo de la tecnología informática, especialmente en el área de sistemas artificiales inteligentes y expertos, las simulaciones por ordenador y el modelado pueden proporcionar las herramientas predictivas del futuro. No solo las computadoras ayudan a recolectar y almacenar datos, sino que también nos ayudan a entender mejor la fuente focal de un fallo de equipo.
Sin embargo, la productividad del mantenimiento se puede mejorar drásticamente mediante la planificación y programación de las actividades de mantenimiento. Durante los últimos 20 años, la mayoría de los fabricantes sólo se han centrado en reducir los costos en los procesos de fabricación para mantenerse competitivosy producir a bajo costo. Este esfuerzo, aunque produjo algún aumento de productividad mensurable, retrasó la oportunidad de obtener el máximo beneficio adicional en la productividad general, ya que el mantenimiento a menudo fue excluido de estos planes de mejora. Claramente, también es importante integrar el programa de mantenimiento en esta agenda de mejora.
Otra preferencia para aumentar el nivel de productividad de mantenimiento es la externalización para los socios de mantenimiento. La asociación con el personal de mantenimiento profesional da a una empresa la ventaja de abordar estos problemas con los expertos que enfrentan y cumplir con estos desafíos sobre una base diaria. Además, la externalización también permite a una empresa obtener un mayor control sobre los resultados de mantenimiento. Sin embargo, es importante destacar que los siguientes elementos clave deben ser destacados para lograr el beneficio óptimo de estas actividades de outsourcing:
- Las mediciones de rendimiento se desarrollan y se comunican claramente
- Se establece el mantenimiento planificado como el foco de la operación
- El mantenimiento se convierte en una ventaja competitiva
- Tanto el fabricante como el contratista de mantenimiento desean una relación mutuamente beneficiosa
- Se establecen las mejores prácticas de mantenimiento
En el escenario de asociación de mantenimiento, las garantías de rendimiento y las metas de mejora continua proporcionan un mayor control sobre los resultados de mantenimiento y garantizan que se están alcanzando los objetivos de producción.
Por lo tanto, ¿surge otra pregunta acerca de cuándo tenemos que comenzar nuestro programa de mantenimiento? El enfoque tradicional de la ingeniería de capital y las organizaciones de proyectos se mide en dos objetivos clave: estar a tiempo y estar en el presupuesto. Esas medidas obligan inevitablemente a los equipos del proyecto a concentrarse en el costo total instalado. Contrario a esto, el grupo de mantenimiento y confiabilidad centra su esfuerzo en equipos que están en funcionamiento y su preocupación es más en la disponibilidad de la máquina, la confiabilidad y evitar el tiempo de inactividad.
La importancia del mantenimiento eficaz tendrá un gran impacto en la rendición de cuentas global de una empresa. Al reducir el costo directo e indirecto del fallo del equipo, el concepto de productivo, eficaz y rentable puede lograrse a partir del programa de mantenimiento.
Devolución de activos = Ingresos ——————————– (1)
Valor del activo
Ingresos = Precio X Volumen ——————————– (2)
Volumen = Máx. Capacidad X Eficacia general del equipo ————- (3)
El mantenimiento efectivo tiene un efecto positivo sobre la ecuación (1), (2) y (3). El mantenimiento mejorado ayuda a mejorar el ROA al reducir la necesidad de costosas actualizaciones de capital para aumentar la producción.
Observaciones finales
El requisito para el proceso de mantenimiento ha cambiado drásticamente desde el viejo concepto de “arréglalo cuando falle” a un enfoque más complejo, que implicó la estrategia de mantenimiento adoptado de un enfoque más integrado. Hoy en día, la dirección ha tomado conciencia de que el mantenimiento también será parte de la toma de decisiones de inversión, lo que lleva a los gerentes a tener en cuenta las fuentes de financiación y el impacto de la inversión en las líneas de crédito y los impuestos y no sólo centrarse en el costo inicial y la depreciación.
Referencias
Dunn, S (1998), ReinventingtheMaintenanceProcess – Towards Zero Downtime, Queensland MaintenanceConference
Moubray JM, (2000), Maintenance Management – A New Paradigm, Maintenance Resources.Com
Tesdahl, SA and Tomlingson PD, (1999), BreakthroughMaintenanceStrategyforthe 21st Century, Equipment Management
Williamson, RM (2000), BreakthroughStrategyforChangingBehaviors, MaintenanceResources.Com