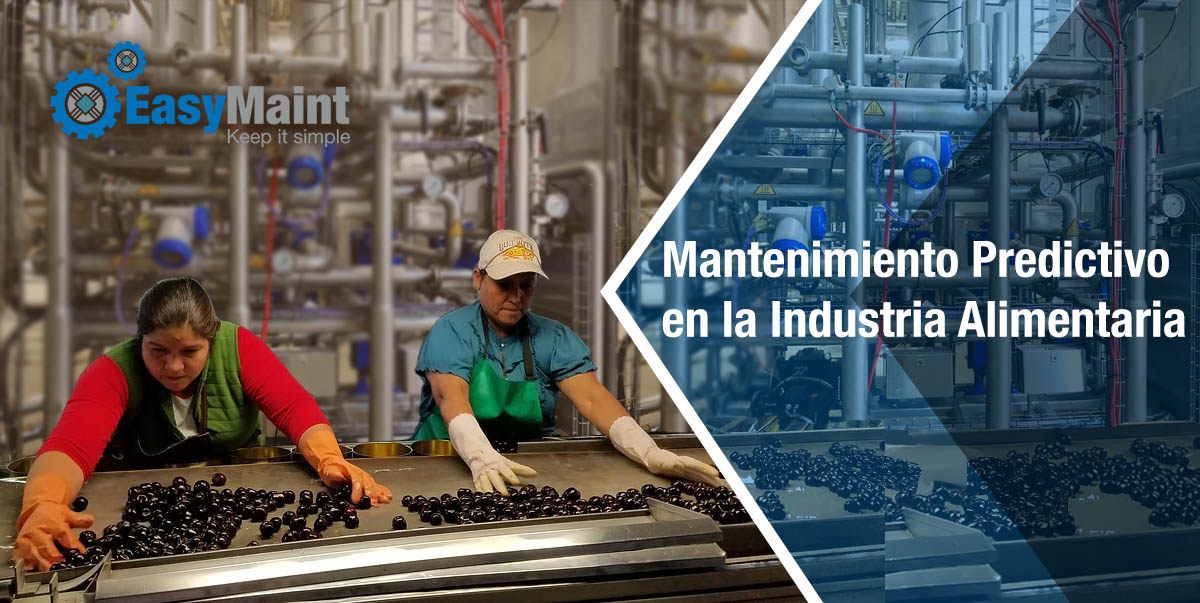
La recopilación y análisis de datos de una base más amplia de equipos instalados debería ayudar tanto a los procesadores como a sus OEM.
Por Kevin T. Higgins, Editor
Nov 09, 2017
El tiempo de inactividad de la máquina, en general, es un evento aleatorio, lo que explica por qué la predicción de fallas sigue siendo un objetivo difícil de alcanzar en la fabricación de alimentos.
El mantenimiento predictivo es ciertamente posible, como lo demuestra su implementación en otras industrias. El gran obstáculo es el costo: establecer un programa interno de mantenimiento predictivo «puede fácilmente exceder los $ 100,000 USD solo para la puesta en marcha», según las autoridades de SKF Inc., Lansdale, Pensilvania. También requiere otro bien preciado: el tiempo. Las rutinas de mantenimiento basadas en el tiempo no son una panacea para los averías aleatorias, pero son evidencia de un plan para reducir su frecuencia.
Los costos de los termómetros infrarrojos, las sondas ultrasónicas, los monitores de vibración y otras herramientas de monitorización del estado están disminuyendo, aunque su precio aún puede exceder los presupuestos de los fabricantes de alimentos y bebidas más pequeños. Los sensores inteligentes que proporcionan una retroalimentación similar pueden hacer que la asequibilidad no sea un problema, pero si solamente generan más información, entonces no están acercando a la industria al mantenimiento predictivo.
La predicción de fallas para una máquina específica puede ser un desafío más allá del alcance de los analizadores de vibración y de temperatura. Se necesita tener una muestra amplia de información para una predicción confiable. Los fabricantes de equipos teóricamente podrían determinar los primeros signos de advertencia de un colapso, pero los fabricantes de equipos originales rara vez pueden comparar el rendimiento una vez que las máquinas salen de sus tiendas. Eso está comenzando a cambiar.
Después de dos años de recopilación de datos con un sistema de administración de mantenimiento computarizado (CMMS), el procesador de fiambres West LibertyFoods generó una base de datos impresionante sobre el rendimiento de 50 máquinas cortadoras de alta velocidad. Analizar los datos era otra cuestión, por lo que las señales de falla y los datos de reparación se exportaron a una hoja de cálculo de Excel y se entregaron al OEM de las cortadoras. El vendedor pudo identificar tres procedimientos de mantenimiento que incluían muchos eventos de inactividad.
Tetra Pak Inc. (www.tetrapak.com/us) está adoptando un enfoque más expansivo con un servicio de monitoreo remoto que involucra su base global instalada de más de 5,000 máquinas de empaque. Comienza con capacidades mejoradas de detección en las máquinas, aumentando los sensores que ya están instalados. Se han adaptado dos o tres sensores adicionales a cada servo motor, según Paul Grainger, gerente de cuentas clave en la sede central de Tetra Pak en Denton, Texas. Con la ayuda de dos y hasta más de 20 servos en cada máquina, no es difícil llamar a esos sistemas de empaquetado máquinas inteligentes.
Los datos del sensor se cargan en un servidor en la nube y son analizados por expertos del servicio en Londres. Cuando el calor o la vibración de un componente comienza a moverse dentro de un cierto rango, se avisa al fabricante del tiempo previsto para la avería, en función de las fallas de la máquina en la red. Si el fabricante se suscribe al servicio de soluciones de cuidado de plantas de Tetra Pak, se envía un técnico con Microsoft HoloLens, que vincula al técnico con los expertos de Londres y guía el mantenimiento preventivo.
HoloLens agrega un toque de Buck Rogers al servicio. Los técnicos de campo se comunican en tiempo real con los expertos de Londres a través de Skype, que también es propiedad de Microsoft. Grainger minimiza la óptica, sin embargo. «No es la inversión de hardware», dice. «El valor proviene de los algoritmos que hemos desarrollado, la capacidad de comparar con equipos similares y la competencia del personal dedicado en la interpretación de los datos».
En una prueba piloto, un procesador estadounidense de leche fluida cuantificó un ahorro de 48 horas en la recuperación de un evento de inactividad, gracias a un técnico de campo equipado con HoloLens. Con el arnés que les brinda a los expertos una visión en tiempo real de la maquinaria y los diagramas de visualización de tecnología y otros materiales de soporte, se simplificó y aceleró el análisis de causa raíz. De lo contrario, un «proceso de escalamiento» para identificar el área del problema, emparejarlo con el experto apropiado y enviar a ese individuo al sitio habría retrasado el restablecimiento de la máquina en dos días.
El servicio se limita al equipo Tetra Pak, aunque está evolucionando a «un enfoque de toda la planta» para incluir maquinaria robótica y otros equipos sofisticados, señala Grainger. La firma está «explorando posibilidades» de extender el servicio a los equipos y centros de servicio técnico de otros OEM.