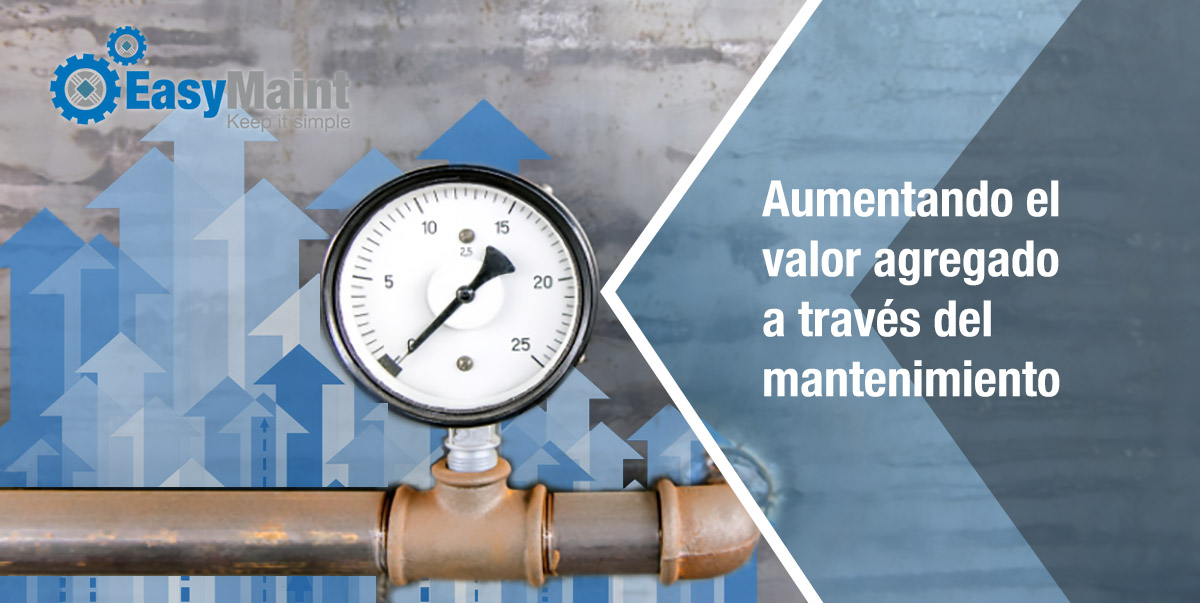
El mantenimiento ha sido considerado un mal necesario en la instrumentación de la planta operativa. Con la consideración correcta, sin embargo, el mantenimiento, incluida la verificación, la calibración y los controles de rutina, puede dar un valor agregado real a través de una mayor confiabilidad, tiempo de actividad y optimización de las instalaciones de la planta. Neil Ritchie y Mark Allinson de ABB hacen hincapié en que una buena estrategia de operaciones solo puede funcionar si los instrumentos de primera línea se aplican y se les da mantenimiento correctamente.
Administrar un instrumento para garantizar niveles uniformes de eficiencia y rendimiento a lo largo de su vida útil puede ser una tarea compleja que requiere la consideración de una multitud de factores diferentes. Por esta razón, es imperativo contar con un plan de mantenimiento eficaz elaborado desde el principio que le permita identificar rápidamente y abordar cualquier desviación o deterioro en el rendimiento.
Los planes de mantenimiento deben abordar tres cuestiones clave:
- Actividades de mantenimiento: ¿Qué acciones específicas se necesitan? ¿Qué técnicas de monitoreo se usan?
- Experiencia: ¿Tengo las habilidades adecuadas? ¿Cómo administro el conocimiento y el aprendizaje? ¿Cómo puedo desarrollar personas para que cumplan con los estándares modernos?
- Tiempo: ¿Cuándo realizo cada actividad? ¿Cómo planeo y organizo para las necesidades futuras? ¿Cómo evito el mantenimiento excesivo del equipo?
Los ingenieros de mantenimiento solían tener mucho en común con los bomberos. Cuando algo, en alguna parte de una planta fallaba, actuaban para solucionar el problema y hacer que la producción volviera a la normalidad. Pero en la actualidad, el mantenimiento consiste cada vez más en evitar problemas antes de que comiencen y este enfoque predictivo es posible gracias, en gran medida, a la aparición de sistemas de control e instrumentación más inteligentes, junto con un buen programa de gestión del ciclo de vida de un equipo.
El mantenimiento predictivo no se trata solo de prevenir fallas catastróficas. En toda la gama de industrias de proceso, donde las especificaciones del producto son extremadamente ajustadas y la presión para minimizar los costos operativos es enorme, poder detectar los primeros signos de deterioro del rendimiento y planificar e iniciar actividades de mantenimiento en el momento adecuado puede marcar la diferencia entre el beneficio y pérdida.
Tomemos, por ejemplo, el consumo de energía. La industria en general vio los precios del gas y la electricidad aumentar en un 47% y un 34%, respectivamente, en 2005, según la Federación de Empleadores de Ingeniería. Usar la instrumentación adecuada para detectar el desperdicio, como fugas de líneas de vapor o recipientes a temperaturas excesivas, ahorra energía y ayuda a mitigar el costo adicional. El monitoreo correcto del flujo puede permitir a los operadores de calderas controlar la producción para que coincida con la demanda, en lugar de gastar vapor a través de la sobreproducción. Mantener los instrumentos optimizados, precisos y confiables asegurará que los ahorros a través del control de desperdicio y el control del proceso se realicen en la línea inferior.
La instrumentación moderna desarrollada por ABB proporciona avances tecnológicos que pueden ser una ayuda para las prácticas de mantenimiento predictivo. Un ejemplo es la tecnología para redes de cable único que transportan datos, permitiendo que muchos dispositivos tales como flujo, presión, analizadores, estaciones de E/S, motores, accionamientos y controladores de proceso se conecten juntos por una sola línea de transmisión o línea de datos. El acceso a la información puede hacer que la toma de decisiones sea más rápida, con acceso a alarmas instantáneas, y puede ayudar con el desarrollo del conocimiento sobre el rendimiento de la planta.
Los mejores consejos para operar un buen programa de gestión del ciclo de vida de los equipos son:
- Selección. El punto de partida para una instrumentación confiable y precisa es elegir el dispositivo adecuado para el trabajo. Aunque parece una afirmación obvia, hay muchos instrumentos instalados que no cumplen con los requisitos o no ofrecen la especificación para ofrecer beneficios reales al negocio.
En particular, esté atento a las opciones de bajo mantenimiento. Algunos tipos de equipos están diseñados específicamente con protección incorporada contra entornos arduos. Por ejemplo, puede valer la pena optar por un tipo de transmisor de temperatura que está completamente en aislado, lo que hace que el transmisor sea mucho menos vulnerable a la vibración, la entrada de contaminación y los cambios en la temperatura ambiente que pueden causar cambios en otros modelos.
Al seleccionar los materiales de construcción para un instrumento, recuerde considerar todos los posibles escenarios operativos. Claramente, el proceso principal debería ser la consideración principal, pero otros factores también son importantes. Por ejemplo, piense en cualquier producto químico de limpieza que pueda usarse. Haga preguntas como, ¿puede la instalación estar sujeta a presiones o temperaturas fuera de la clasificación del instrumento? ¿Se puede crear un vacío en condiciones de falla? La etapa de especificación del instrumento puede, en algunos casos, aumentar significativamente la vida útil de un instrumento y proporcionar una instalación mucho más segura.
La selección, sin embargo, va más allá del producto mismo. El proceso de selección también debe considerar el respaldo del servicio y el soporte técnico ofrecido por el proveedor. ¿Hay ingenieros de servicio local disponibles para ayudar cuando sea necesario? ¿Puede el proveedor ayudar a administrar o contribuir a su programa de ciclo de vida? Lamentablemente, estas consideraciones a menudo se pasan por alto, y solo pasan a primer plano cuando ocurre una crisis o cuando se incurre en una alta penalización por un error.
- Instalación y puesta en marcha. Es importante que cualquier dispositivo se instale y ponga en marcha correctamente. Esto requiere no solo seguir las especificaciones operacionales del fabricante, sino también considerar los requisitos de mantenimiento posteriores a la instalación. Los instrumentos de difícil acceso generalmente se ignoran o se pasan por alto al realizar actividades de mantenimiento. Por lo tanto, los dispositivos deben instalarse y ponerse en servicio para cumplir con las especificaciones de diseño precisas y ser de fácil acceso.
Otra consideración clave es el entorno operativo. Factores tales como altas temperaturas ambientales y humedad excesiva, por ejemplo, pueden acortar drásticamente la vida útil de un instrumento. Consulte el manual de instrucciones o la guía de instalación para obtener ideas prácticas sobre cómo evitar problemas operativos. Mejor aún, utilice la experiencia del servicio del fabricante del instrumento y los ingenieros de aplicaciones, que contarán con una gran cantidad de conocimientos prácticos y experiencia para ayudar en la puesta en servicio. La optimización de la configuración de un instrumento desde el principio puede ayudar a maximizar su vida operativa al reducir el riesgo de problemas posteriores durante la operación.
- Actividades de registro y seguimiento. La presión sobre los recursos y la proliferación de instrumentos en toda la planta significa que el registro de historiales de servicio a menudo se descuida o se implementa tarde en el ciclo de vida de un producto.
Sin embargo, prestar atención a estas áreas desde el principio puede ofrecer beneficios reales y ahorros de costos a lo largo del ciclo de vida de un producto. Por ejemplo, anotar los parámetros de configuración originales de un instrumento puede mejorar el tiempo de recuperación si ocurre una crisis. Muchos instrumentos ahora tienen memoria para permitir que estos parámetros se guarden independientemente de la memoria de trabajo normal del instrumento. Busque los instrumentos que ofrecen esta característica.
Las acciones de servicio posteriores también deben registrarse y planificarse, no solo para satisfacer las necesidades del instrumento sino también para cumplir con los requisitos reglamentarios y evitar el mantenimiento excesivo de un dispositivo. Al registrar y rastrear actividades en «tiempo real», se reduce la necesidad de auditorías regulares y costosas para establecer el estado actual del ciclo de vida y el estado de los instrumentos. Obtener la documentación correcta no solo es importante para administrar un buen programa de mantenimiento con ventajas directas para planear, sino también para cumplir con los estándares regulatorios, de seguridad y ambientales.
- Planificación y coordinación. Aunque el mantenimiento de planificación no es una actividad nueva para la mayoría de los gerentes de mantenimiento, la vida útil inherentemente más larga de un equipo más confiable y robusto requiere un enfoque diferente. Muchos productos pueden ofrecer un servicio confiable durante 15 a 20 años con una buena rutina de mantenimiento, pero también se deben tener en cuenta las características y los beneficios adicionales que ofrece la tecnología más nueva.
En términos simples, el programa de mantenimiento debe estar diseñado para tomar las decisiones correctas para mantener, respaldar y actualizar en el momento justo.
La planificación del ciclo de vida satisface esta necesidad al ofrecer un plan basado en la investigación, experiencia y conocimiento del fabricante superpuesto con el conjunto de habilidades y el producto de servicio. Por ejemplo, la calibración puede realizarse anualmente para garantizar un rendimiento óptimo, pero varios componentes portátiles, como los ventiladores, requieren reemplazo antes de que puedan introducir mediciones o controlar las ineficiencias.Una buena planificación elimina la sobrecarga de la planta con intervenciones innecesarias, costos y atención causados por el mantenimiento excesivo de los productos. Los fabricantes de renombre como ABB ofrecen programas completos de gestión del ciclo de vida que incluyen programas de actividad planificados, ya sean para que el cliente los realice o que puedan ser entregados por ingenieros certificados.
- Recursos y capacidades. Administrar el personal para satisfacer las necesidades de un complejo y variado tipo de instrumentos y equipos puede ser difícil. No solo al reclutar para alcanzar la capacidad adecuada de la persona, sino el desarrollo continuo del personal para mantenerse al día con las mejores prácticas actuales más una gama cada vez mayor de necesidades ambientales, técnicas y de rendimiento.
Un programa de mejora continua que utiliza programas de desarrollo personal y capacitación es solo un elemento. Mantenerse en contacto con la tecnología también requiere que el personal tenga exposición operacional para desarrollar experiencia y permitir el aprendizaje.
A veces, las áreas especializadas de tercerización son la única solución. Sin embargo, esto aún puede ofrecer beneficios significativos en términos de costos de capacitación reducidos, retención de personal y mantenimiento de un gran número de empleados.
Alternativamente, muchos fabricantes, incluido ABB, ofrecen programas de capacitación y talleres para mantener a sus clientes en contacto con las prácticas y tecnologías cambiantes.
- Hacer el trabajo correctamente. Hacer el trabajo correcto en el momento adecuado con las habilidades adecuadas es una forma segura de evitar costos más altos y reducir el tiempo de inactividad, al tiempo que extiende la vida útil del instrumento y maximiza la eficiencia. La calibración es un buen ejemplo. Muchos vendedores de transmisores de presión afirman que sus productos requieren recalibración cada cinco años, pero las cifras citadas se basan en un conjunto específico de condiciones que pueden tener poco que ver con las condiciones en el sitio. En muchos casos, el usuario solo sabrá la frecuencia de calibración correcta con certeza si él mismo la calcula.La frecuencia de calibración depende de tres cosas: la aplicación, el rendimiento requerido y las condiciones de operación.
La aplicación es importante porque afecta la precisión necesaria. Algunas aplicaciones tienen una relación directa con la seguridad o la eficiencia de la planta y requieren una cifra de alto rendimiento, del orden del 0.5% de lectura o mejor. Es posible que otras aplicaciones no exijan un rendimiento muy alto. Si todo lo que se necesita es indicar que el nivel del agua en un tanque está aproximadamente en el centro, por ejemplo, alrededor del 10% de la luz puede ser lo suficientemente bueno.Las condiciones de operación son otro factor vital. En el caso de nuestro ejemplo del transmisor de presión, por ejemplo, la presión estática, la temperatura ambiente y la estabilidad de la densidad del producto tendrán una figura de error asociada o un efecto en la lectura. Otros parámetros pueden ser igualmente importantes para otros tipos de instrumentos.
Luego, calcule el error total probable. Esto está determinado por una fórmula que incorpora términos para la precisión base citada del dispositivo y los probables efectos de la presión estática y los errores de temperatura en la precisión del rendimiento.
Determine la estabilidad por mes. El proveedor debe proporcionar los datos necesarios para un instrumento en particular. Normalmente, la estabilidad se expresará durante un período de tiempo dado, como 36 meses.
La frecuencia de calibración viene dada por el rendimiento requerido menos el Error Probable Total, dividido por la estabilidad por mes. Esto determina la frecuencia con la que se debe verificar la calibración para mantener la precisión deseada.
- Evaluar y reevaluar. Un buen programa de ciclo de vida necesita una evaluación continua. Un programa diseñado adecuadamente tendrá dicha evaluación incorporada en el seguimiento y la grabación de la información, en lugar de tratarse como una actividad separada, más frecuente y de alto costo. Las auditorías iniciales pueden enfocar las actividades en las áreas críticas de negocios correctas. El programa de ciclo de vida real implementado también debe evaluarse periódicamente, desafiando los métodos y prácticas empleados en lugar de solo centrarse en las necesidades del instrumento específico. Este enfoque de aprendizaje garantizará que las técnicas modernas y los beneficios de las nuevas tecnologías se tengan en cuenta en todo el plan.
Por ejemplo, muchos medidores de pH se benefician de una limpieza regular, por lo que en determinadas circunstancias, puede ser mejor instalar uno con una función de autolimpieza automática. Este tipo de sensor utiliza un sistema de lavado a presión y requerirá un cambio en la aplicación del mantenimiento. Además, el análisis de la raíz de la causa debe ser parte de las actividades de mantenimiento correctas. Este es un enfoque bien documentado para analizar fallas y buscar formas de mejorar o descartar el potencial de una recurrencia. Esto podría estar dentro de las necesidades de diseño, acceso o mantenimiento del producto. Este mismo enfoque se puede aplicar a las prácticas llevadas a cabo. Por ejemplo, mantener un inventario de repuestos o un instrumento completo de «repuesto dinámico» en el modo de espera para emergencias puede ser una tarea valiosa para evitar largos períodos de inactividad del error de medición.
Caminar por el sitio puede actuar como una forma sencilla de encontrar oportunidades donde un buen mantenimiento puede mejorar la operación de la planta y, a menudo, puede actuar como un sustituto de un programa cuidadosamente planificado. Un ejemplo es comprobar el rendimiento de la planta de aire comprimido, donde se estima que las fugas le costaron a las empresas del Reino Unido el 30% de sus costos de energía.
Por supuesto, existen formas tradicionales de detectar fugas, como escuchar silbidos o revestir juntas con solución de jabón y buscar burbujas. Al buscar fugas es útil saber que hay algunos componentes de un sistema de aire comprimido que son especialmente vulnerables, como cilindros neumáticos, bridas, filtros, herramientas, prensas y martillos de caída. Pero incluso si sabe por dónde empezar a buscar, las encuestas de sitios son laboriosas, tardan mucho tiempo y deben repetirse periódicamente.
Este tipo de encuesta puede ser costosa y también detectará fugas que son lo suficientemente grandes y accesibles para que un operador humano las detecte. Como regla general, este enfoque deja sin reparar el 10% de las fugas en un momento dado, lo que es preocupante si considera que un solo orificio de cinco milímetros en una línea de aire cuesta alrededor de £ 1,400 por año.
Una solución es usar medidores de masa térmica para medir el consumo de aire comprimido. En comparación con los operadores humanos, los medidores de masa térmica pueden detectar pequeñas fugas. También operan continuamente, por lo que pueden indicar un problema potencial a medida que se desarrolla, en lugar de esperar a la próxima encuesta. Una vez en su lugar, pueden ayudar con otros aspectos de una buena administración, como controlar la cantidad de aire comprimido utilizado por cada consumidor.
- Salud y seguridad. Si bien este tema es último en nuestra lista de consejos, sin duda debe ser prominente en el pensamiento de todos al abordar cualquier actividad de mantenimiento. Seguir los procesos y las recomendaciones correctos e incorporar la salud y la seguridad en el cultivo de plantas y cualquier actividad asociada puede reducir significativamente el riesgo.