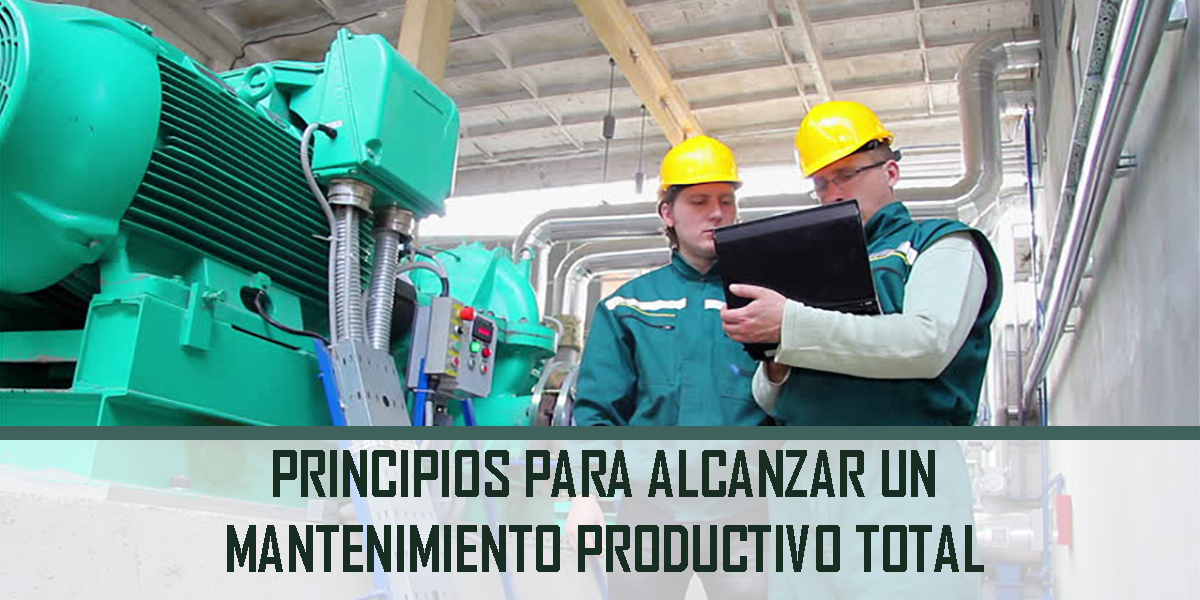
Responsabilidad compartida
Casi todos los procesos de producción industrial se llevan a cabo con la ayuda de equipos. De esta manera debemos centrarnos en los equipos si deseamos aumentar la productividad. El principio básico del Mantenimiento Productivo Total (TPM) es que todos los departamentos de una empresa deben comenzar a sentirse parte del mantenimiento. Hay que tomar en cuenta que esto también abarca la mejora de los equipos. Según la filosofía del TPM, una máquina, en muchos casos, no funciona al cien por ciento en el momento en que fue comprada. Después de la compra, es necesario adecuarla a nuestros procesos de producción y esa es la base de una mejora continua.
Para alcanzar los objetivos de un TPM se debe tener una actitud preventiva y responsabilidad compartida, es lo que se llama mantenimiento autónomo. La implementación de un programa formal de mantenimiento preventivo se considera como el paso siguiente.
Aumentar la conciencia
«La implementación de TPM comienza con el aumento de la conciencia de las pérdidas ocultas», explica Van Kollenburg. «Un ejemplo es una falla de una máquina, o tiempo necesario para una configuración de la máquina. También si una máquina no puede funcionar a la velocidad que requiere el proceso, o si se entregan productos con calidad inferior, todo esto se considera como actividades deficitarias.
En un proceso ‘sin pérdidas’, la efectividad total del equipo (OEE) o de todas las máquinas debe estar en el 100%. En ese caso, cada máquina siempre opera a la velocidad requerida por los procesos y se entregan sólo productos de buena calidad.
En la realidad, el OEE a menudo sólo alcanza el 40-50% de su efectividad. El objetivo de TPM es elevar el OEE gradualmente, por cada máquina, hasta llegar al menos al 80% de su capacidad.
Mejora continua
En muchas ocasiones los mantenimientos se llevan a cabo de manera atrasada. Este problema es parte de la reorganización del piso de trabajo, que se llama Total CleanOut. Y este es un gran paso para implementar un TPM basado en la mejora continua.
En ese momento se forma el primer equipo de trabajo multidisciplinario, que comienza a abordar un problema específico que limita el OEE. El proyecto que llevan a cabo se llama una actividad de grupo pequeño o SGA. En un equipo de SGA por lo general hay tanto operadores de máquinas como mecánicos, y además inspectores de calidad y/o administradores de logística. La ventaja es que todo el grupo comienza a sentirse responsable de su máquina o de una línea de producción.
Propietario
El equipo SGA se convierte en propietario del rendimiento de sus máquinas. Esto da lugar a un cambio cultural. Por ejemplo, «operar, reparar», se sustituye por «nosotros, como operador e ingeniero, compartimos la responsabilidad de mantener nuestra instalación funcionando».
Los problemas, que deben ser tratados por el equipo de SGA, se seleccionan a través de un análisis de Pareto. Posteriormente, el equipo SGA buscará la causa raíz del problema. Un diagrama de Ishikawa puede ser de gran ayuda para mapear las causas y consecuencias en una estructura de espina de pescado.
Cuando el equipo de SGA ha detectado la causa de la raíz de un problema, enviará una propuesta de solución a la alta dirección. Se debe incluir un análisis costo-beneficio. Si la solución es aprobada, se implementará. Finalmente, se comprobará si la solución del problema mejora el OEE.
Paso a paso
Después de eso, el equipo de SGA continúa atacando el siguiente problema que más limita al OEE. De esta manera, el OEE se mejora paso a paso.
Sin embargo, este ciclo de mejora es sólo el primer paso de TPM. El siguiente paso se refiere a la introducción del mantenimiento autónomo. Después de eso, el mantenimiento no es sólo una tarea para los técnicos, sino que implica a todos, dentro de los límites de su experiencia. Por ejemplo, los operadores deben inspeccionar sus máquinas regularmente, y en ocasiones ellos mismos pueden limpiar y/o lubricar los equipos.
Posteriormente, se elaborará un calendario para el mantenimiento preventivo (y en ocasiones también predictivo). Más adelante, se pasa a un programa de formación, para que todos los empleados conozcan los principios de TPM y la mejora continua, no sólo de manera general, sino también en relación con su propio lugar de trabajo.
Metas
En primer lugar, se determina qué pérdidas deben reducirse en una fábrica durante el próximo ciclo de operación. A continuación, estas prioridades se traducen en Indicadores de Desempeño Clave, primero para el nivel intermedio y después para el nivel operativo. La idea es que finalmente todo el mundo debe saber cómo puede contribuir personalmente para cumplir con la agenda de mejora continua.