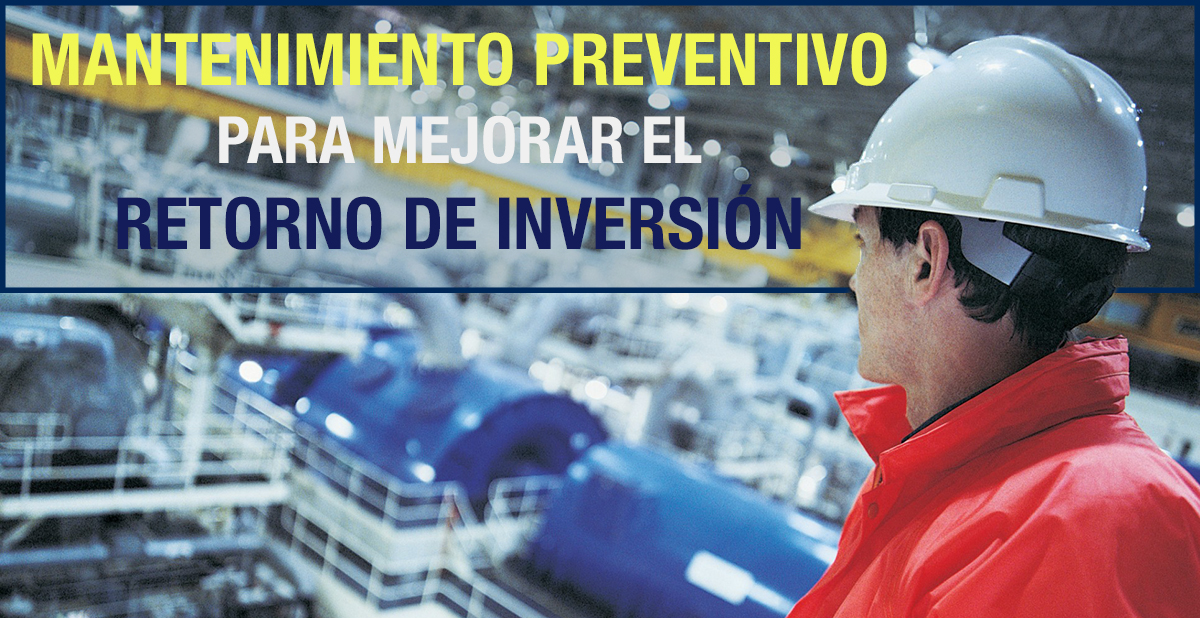
Por John Kravontka, CMRP, Soluciones de Fabricación Fuss& O’Neill
La mayoría de las cosas en nuestras vidas requieren mantenimiento. Automóviles, trenes, aviones, camiones, casas, puentes, caminos, maquinaria industrial – ninguno de ellos puede continuar funcionando correctamente si no se mantienen debidamente. Incluso nuestros propios cuerpos requieren mantenimiento a través de una buena alimentación y ejercicio.
Pero, ¿qué es el mantenimiento? Algunas personas piensan que se trata de arreglar las cosas, como reparar un neumático desinflado. Pero en realidad, cuando una pieza de equipo necesita ser reparado, es una indicación de que el mantenimiento no ocurrió. La definición que da el diccionario Webster sobre mantenimiento puede sorprender a algunas personas: el mantenimiento son “aquellas acciones necesarias para el cuidado de maquinaria, un edificio, etc., para mantenerlo limpio y en buen estado de funcionamiento, para prevenir daños debidos al uso constante“. Realmente se trata de todos los mecanismos para mantener algo antes de que falle o se deteriore. Se trata de prevención.
En todo el mundo, incluso en los Estados Unidos, el mantenimiento tiende a ser manejado muy mal. La mayoría de las empresas e instituciones o bien no mantienen sus activos de capital o postergan el mantenimiento en algún momento en el futuro. Típicamente, ese tiempo nunca llega. Y el mantenimiento pobre o diferido cuesta a las empresas millones de dólares cada año.
El motor de la industria
Por supuesto, no es sólo en nuestras vidas personales donde el mantenimiento importa. La economía de un país depende de la eficiencia y efectividad de la industria. Lamentablemente, cuando se trata de mantenimiento, las empresas no están midiendo los costos excesivos por reparaciones. Como resultado, su equipo funciona mal, con una producción costosa que no pueden cargar a los productos o servicios que se entregan a los clientes. Los gastos de mantenimientos correctivos pueden ocurrir en cualquier momento. El mal desempeño del equipo cuesta a los fabricantes enormes cantidades de rentabilidad cada año debido a que el equipo no produce al nivel para el cual fue diseñado. El tiempo extra de trabajo de la producción (para ponerse al día), los costos adicionales de la materia prima (chatarra), el tiempo de ejecución acelerado para compensar la mala calidad, el equipo adicional y los costos adicionales de energía constituyen parte de los costos adicionales que las compañías acumulan innecesariamente cada año. Todo esto se debe a las malas prácticas de mantenimiento.
La diferencia entre una empresa manufacturera que genera ganancias y tener que cerrar sus puertas está a menudo en manos de la organización de mantenimiento y su capacidad para ser proactiva en lugar de reactiva. El mantenimiento reactivo es muy costoso, y conduce al mal funcionamiento del equipo.
Con el tiempo, los fabricantes comienzan a aceptar el mal funcionamiento de los equipos, un proceso que a menudo pasa desapercibido porque sucede muy lentamente. Trabajan en torno a los equipos con fallas y reaccionan a los problemas de calidad, creyendo que esta es la única manera que pueden mantener los niveles de producción. A pesar de que pueden comenzar a quedarse atrás en el cumplimiento de sus objetivos de producción, algunas empresas racionalizan el mantenimiento hasta que la planta de producción debe cerrar un tiempo por mantenimiento general, ya que los mantenimientos se estuvieron aplazando durante mucho tiempo. Sin embargo, si el equipo presenta una falla, las paradas pueden ser menores, pero se tendrán problemas de calidad de los productos o una producción reducida. En este tipo de casos, se requiere una planificación de mantenimiento, incluso con algún tiempo de inactividad.
Una solución inmediata
El desafío que enfrentan los fabricantes es cómo implementar un programa de mantenimiento que proporcionará un retorno de la inversión inmediato, ya que puede tardar hasta cinco o 10 años en formar personal de mantenimiento e introducir programas para llevarlos a cabo.
El primer paso es estimar lo que el deficiente rendimiento del equipo está costando en una instalación dada. Comenzar a entender lo que significaría la mejora de la producción, calidad y fiabilidad de los equipos en los procesos de fabricación. Los fabricantes, a continuación, verán la gran oportunidad que tienen frente de ellos.
El segundo paso es llevar a cabo una auditoría de mantenimiento. La auditoría permite a las compañías evaluar la efectividad de sus esfuerzos actuales contra un estándar de mantenimiento de clase mundial. La auditoría comienza con una evaluación visual de cómo está funcionando el equipo, monitoreando constantemente ese equipo durante toda la jornada de trabajo y registrando cuán eficientemente está funcionando. A menudo sólo es necesario vigilar el equipo durante unas pocas horas para tener un buen sentido de lo bien que está funcionando y dónde se pueden encontrar problemas potenciales, tanto en términos de operaciones a corto y largo plazo. La evaluación también debe contemplar al departamento de mantenimiento de acuerdo con un estándar de clase mundial, para permitir a la organización ver dónde está ubicado su funcionamiento y dónde necesita mejorar. La auditoría puede ser llevada a cabo por administradores de mantenimiento internos o consultores experimentados que son expertos en el proceso de mantenimiento.
Una vez completada la evaluación, es necesario elaborar un plan a corto plazo para corregir los problemas identificados durante la fase de auditoría. El plan debe ser creado con el objetivo de que el equipo esté completamente operativo tan pronto como sea posible. Los enfoques de “parches” temporales no son soluciones en absoluto, ya que típicamente llevan a nuevos problemas en el camino, mientras que obstaculizan la productividad en el corto plazo.
Sin embargo, aunque estos pasos iniciales representan un progreso, siguen siendo reactivos. El objetivo de cada fabricante debe ser tener un programa de mantenimiento proactivo. Esto no sucede de la noche a la mañana. Muchas empresas encuentran que necesitan implementar planes de 3 a 5 años para pasar del mantenimiento reactivo al mantenimiento proactivo. Los planes se crean estableciendo metas de producción para el equipo y luego determinando las mejores prácticas de mantenimiento que conducirán a que el equipo sea capaz de alcanzar esas metas. Cada empresa, cada instalación y cada pieza de equipo es diferente, y los planes para cumplir esos objetivos deben construirse en torno a las características únicas y desafíos presentados por la empresa y sus equipos.
Las compañías que tratan el mantenimiento como una prioridad pueden ahorrar millones de pesos al evitar la costosa reparación del equipo, la baja productividad y las pérdidas relacionadas con la seguridad. No es difícil hacer del mantenimiento una parte importante de las operaciones cotidianas, pero a menudo requiere que los líderes de la empresa cambien su forma de pensar. Las empresas que hacen un compromiso con la excelencia en el mantenimiento no sólo ahorran dinero, sino que también crean un mejor ambiente de trabajo, producen un mejor producto y obtienen una ventaja competitiva sobre sus competidores que no entienden la importancia del mantenimiento.