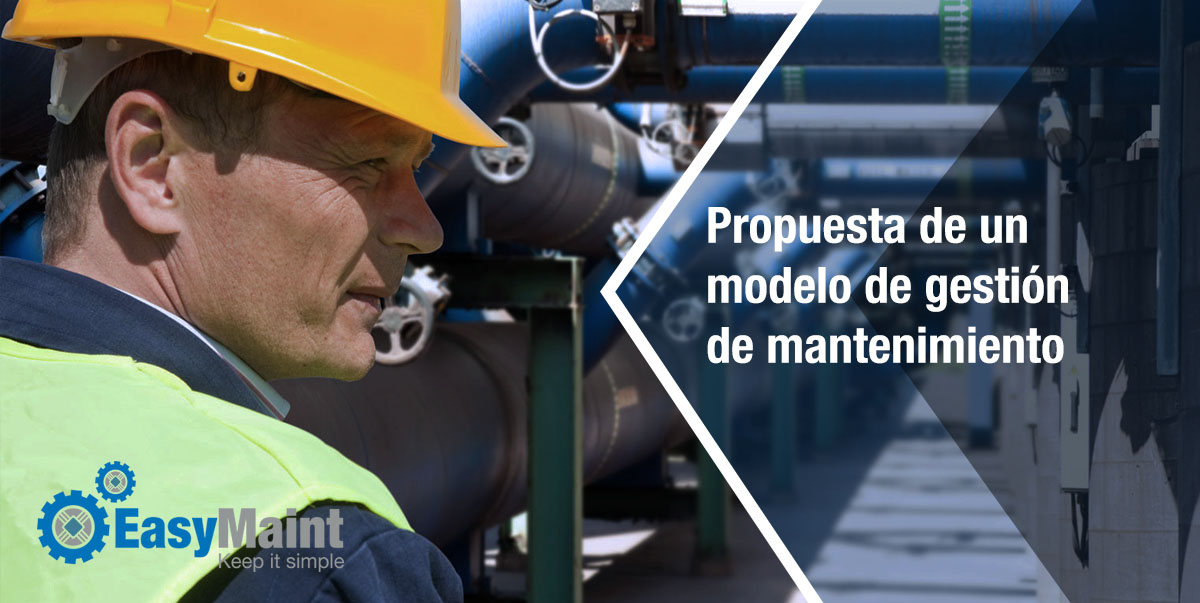
Pablo Viveros1 Raúl Stegmaier1 Fredy Kristjanpoller1 Luis Barbera2 Adolfo Crespo2
1Departamento de Industrias. Universidad Técnica Federico Santa María. Avenida España 1680. Valparaíso, Chile. E-mail: pablo.viveros@usm.cl; raul.stegmaier@usm.cl; Fredy.kristjanpoller@usm.cl
2Departamento de Mantenimiento Industrial. Escuela de Ingenieros. Universidad de Sevilla. Sevilla, España. E-mail: lbm@esi.us.es; adolfo@esi.us.es
Descripción de las etapas del modelo de gestión de mantenimiento propuesto
A continuación se exponen las etapas del modelo suponiendo que la organización ya gestiona, en menor o mayor medida, el mantenimiento.
Etapa 1: Análisis de la situación actual. Definición de objetivos, estrategias y responsabilidades de mantenimiento: En primer lugar, y como paso previo a cualquier actividad, es necesario realizar una evaluación de la situación inicial o existente en Integración de herramientas y habilitantes al sistema informático (ERP, Softwares de MTTO, Software de gestión de MTTO) relación a la gestión del mantenimiento. Este análisis debe realizarse en el caso de que la organización o planta ya disponga de un método más o menos definido de gestión, o más aún, en caso de que no exista algún método o procedimiento destinado a esta labor. Esta evaluación o diagnóstico de la situación actual debe considerar todos aquellos aspectos relacionados con el mantenimiento de equipos de los cuales se disponga información; por ejemplo, aspectos tales como la planificación, programación y ejecución de las tareas de mantenimiento, histórico de fallas, indicadores de tiempo medio entre fallas (MTTF) y tiempo medio de reparación (MTTR), recursos financieros asignados al mantenimiento, impacto económico o en producción (consecuencia de falla del equipo) por parada no programada de la planta (sistema) o subsistema, entre otros.
Para lograr un correcto desempeño en la gestión global del mantenimiento en una organización resulta imprescindible definir previamente los objetivos (metas) que se persiguen, estableciendo una estrategia orientada a esos objetivos y determinando las responsabilidades del personal implicado a nivel operacional y gerencial. El proceso de definición de una estrategia de mantenimiento requiere (Figura 4):
- Determinar, en base a los objetivos corporativos del negocio, los objetivos de mantenimiento, por ejemplo: valores estimados y realistas para los siguientes indicadores de gestión: disponibilidad de equipos, confiabilidad, seguridad, riesgo, etc. Determinar el desempeño o rendimiento actual de las instalaciones productivas, comparándolas con sus respectivas capacidades nominales.
- Determinar los indicadores claves para la evaluación del rendimiento de las instalaciones (Key Performance Indicators-KPIs).
Figura 3. Modelo de gestión de mantenimiento.
Figura 4. Modelo para la definición de la estrategia de mantenimiento.
La gestión del mantenimiento debe conseguir alinear todas las actividades de mantenimiento con la estrategia definida a nivel estratégico o de dirección, táctico y operativo. Una vez que se han transformado las prioridades del negocio en prioridades de mantenimiento, se procederá a la elaboración de la estrategia, de acuerdo con los objetivos. De esta forma se obtiene un plan de mantenimiento genérico en la empresa que se desarrollará y enfocará a aquellos activos considerados críticos, identificados por la etapa 2.
Las acciones a nivel táctico determinarán la correcta asignación de los recursos (habilidades, materiales, equipos de pruebas y medida, etc.) para la consecución del plan de mantenimiento. El resultado final será la creación de un programa detallado con todas las tareas a desarrollar y con los recursos asignados para la realización de las mismas.
Las acciones a nivel operativo deben asegurar que las tareas de mantenimiento se llevan a cabo adecuadamente por los técnicos seleccionados, en el tiempo acordado, siguiendo los procedimientos reseñados y utilizando las herramientas adecuadas.
Etapa 2: Jerarquización de equipos: Una vez que se han definido los objetivos, las responsabilidades y se ha diseñado una estrategia de mantenimiento, resulta de vital importancia discretizar los activos físicos de la organización en base a su criticidad, es decir, su mayor o menor impacto en el sistema productivo global y/o seguridad del sistema (objetivos del negocio).
El análisis de criticidad es un conjunto de metodología que permite definir la jerarquía o prioridades de un proceso, sistema, equipos y/o, según el parámetro de valor conocido como «Criticidad» que es proporcional al «Riesgo», generando una estructura que facilita la toma de decisiones acertadas y efectivas, direccionando los esfuerzos y recursos técnico-económicos en áreas y eventos que tienen mayor impacto en el negocio.
Existen numerosas técnicas cualitativas, cualitativo-cuantitativas y cuantitativas que nos ofrecen una base sistemática sobre la cual clasificar un activo como crítico (C) / semicrítico (SC) / no crítico (NC), basadas en la evaluación probabilística del riesgo y la obtención del número/índice probabilístico de riesgo del activo (PRA/PRN). Los activos con índice mayor serán los primeros en ser analizados. En muchas ocasiones no existen datos históricos en base a los cuales obtener estos índices, en estos casos es posible utilizar técnicas de naturaleza más cualitativa con el objetivo de ir garantizando niveles iniciales adecuados de efectividad en las operaciones de mantenimiento.
El Método Cualitativo está basado en opiniones de especialistas, donde se combinan criterios técnicos y financieros para jerarquizar equipos. Se caracterizan por ser subjetivos y efectivos para procesos simples, por lo que se requieren en algunos casos métodos más rigurosos para validar la información. Por ejemplo, se utilizan como criterios la consecuencia (Alto-Medio-Bajo) y complejidad (Compleja-Mediana-Sencilla), en donde la escala numérica para cada criterio pudiese ser 1-5-10.
Para el caso de modelos de cualitativo-cuantitativo, en este se involucran datos objetivos para generar una guía de criticidad cuantificada según: frecuencia de falla, impactos en producción (por falla), costos de reparación, tiempo de reparación, impactos en seguridad personal e impacto ambiental. El factor cualitativo está representado en generar la escala o criterio que represente los resultados de cada ítem medible, y la definición final de la jerarquización de Criticidad. El riesgo o criticidad se define como el producto de la frecuencia por la consecuencia de la falla. La frecuencia es el número de fallas en un tiempo determinado. Para cuantificar la consecuencia de la falla se utiliza la ponderación de varios factores o criterios de importancia en función de las necesidades de la organización.
Riesgo: Frecuencia x Consecuencia
- Frecuencia: Número de Fallas en un tiempo determinado.
- Consecuencia: (Impacto Operacional x Flexibilidad) + Costos de Mantenimiento + Impacto (Seguridad – Ambiente).
Una vez que los activos están jerarquizados en base a su criticidad, se obtiene la Matriz de Criticidad.
Figura 5. Matriz genérica de criticidad.
El análisis cuantitativo tiene un enfoque numérico y probabilístico que busca cuantificar económicamente las variables que definen la criticidad del subsistema, equipo o componente. Se deben valorizar financieramente variables como: costos directos de mantenimiento (repuestos, H.H., insumos, etc.), impacto económico por indisponibilidad del sistema (pérdida de producción total o parcial según configuración lógica funcional), impactos en seguridad e impacto ambiental.
Esta perspectiva (cuantitativa) utilizada para jerarquizar subsistemas, equipos o componentes en un proceso, es aquella que considera el impacto directo sobre el sistema en términos de la disponibilidad esperada (en función de confiabilidad y mantenibilidad) y costos asociados (función de costos directos, indirectos y oportunidad por falla sistémica).
Existen otros métodos de jerarquización basados en indicadores de confiabilidad y mantenibilidad, tanto para hacer un ranking a nivel de modos de falla como también de equipos y subsistemas.
Conceptualmente, el método de análisis Jack-Knife corresponde a un estudio multicriterio de las distintas variables involucradas, o que inciden en los modos de falla, tales como: frecuencia de ocurrencia de falla (tasa de falla promedio), número de fallas, tiempo fuera de servicio (MTTR), costos asociados, entre otros. El mecanismo en sí de análisis, es un diagrama en dos o más dimensiones, en donde cada una de éstas corresponde a una variable de estudio. En el caso de trabajar con números de falla y tiempo fuera de servicio, en el gráfico se trazan líneas de referencia que denotan el número promedio de fallas y el tiempo promedio de reparación de los modos de falla, generando cuatro cuadrantes. Los modos de falla ubicados en el primer cuadrante son aquellos que poseen un número de fallas mayor al promedio (crónicos) y un tiempo fuera de servicio mayor al promedio (agudos), por lo que son candidatos importantes en la escala de criticidad.
Adicionalmente, se puede(n) trazar una(s) recta(s) de isoindisponibilidad de manera que se identifiquen los modos de falla que generen una indisponibilidad mayor a la planteada/esperada. Para esto, por lo general se utilizan escalas logarítmicas para que las líneas de isoindisponibilidad (D) sean rectas. Para mayor detalle, ver Figura 6, en donde se grafican (escala logarítmica) las coordenadas (Número de fallas y MTTR) de algunos modos de fallas.
Figura 6. Representación gráfica de dispersión Jack-Knife.
Donde:
MTTRi = Tiempo Medio de Reparación del Modo de falla i.
N°i = Número de Intervenciones del Modo de falla i.
N = Número de Modos de falla del Equipo/Sistema.
Promedio del Logaritmo del Número de N Intervenciones de los N modos de falla
Promedio del Logaritmo del Tiempo Medio N – de Reparación de los N modos de falla.
Las propuestas de mejora, según la distribución de los modos de falla/equipos/subsistemas en el gráfico, darán la pauta para enfrentar el problema desde el punto de vista de la confiabilidad, producto de la alta frecuencia de intervención, o bien desde la mantenibilidad, dados los altos tiempo medios de reparación.
En general, existen diversos métodos de jerarquización o identificación de criticidades, en donde la mayoría de ellos evalúan, cualitativa y/o cuantitativamente, el comportamiento de las fallas y sus consecuencias.
Propuesta de un modelo de Gestión de Mantenimiento – Parte 1